Faster, better... C.O.R.E.
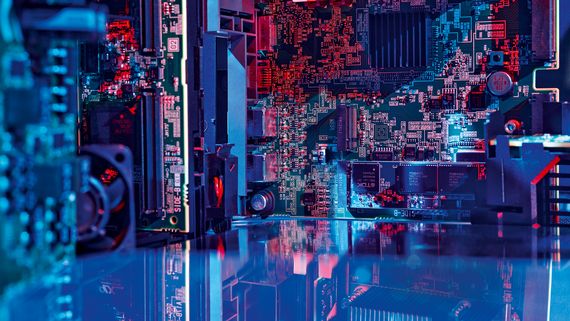
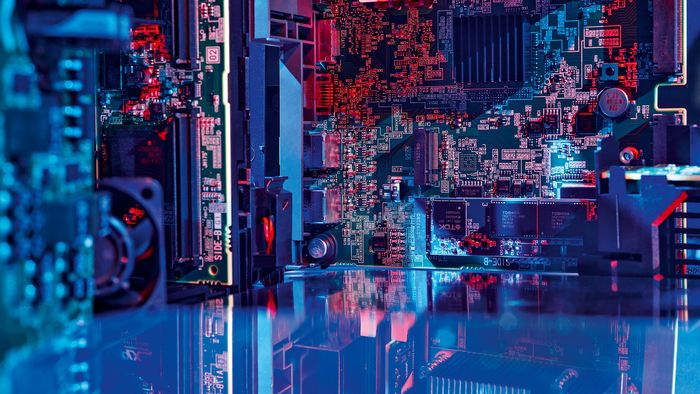

EVERY CNC TECHNICIAN KNOWS THE PROBLEM: searching through a baffling screen of gray boxes and tiny numbers until you finally find the value you want. Next, you have to take off your gloves because the touchscreen only works without them or the keys on the keyboard are too small. And there are instructions printed on paper next to the machine telling you which sub-menus to use to find the production program you need. All of this takes time that would be better spent on the actual work.
But those days are over now that UNITED GRINDING Group has presented its cross-brand hardware and software architecture at EMO 2021 in Milan: C.O.R.E. The name could refer to the core of the machine, but actually is also an acronym for Customer-Oriented REvolution. A revolution that benefits customers—and is already doing so: the system is pre-installed on new machines.
Revolution is a strong word. Is it appropriate to use it? “Yes, certainly,” says Christoph Plüss, Chief Technology Officer (CTO) and organizer of the project. The software departments of all UNITED GRINDING Group brands worked together for six years to develop a market-ready, future-proof system for standardized machine design. “C.O.R.E. is already making our customers’ work much easier,” stresses Plüss.
Multi-touch panel can be operated wearing gloves
One new feature immediately catches the eye. Every new machine with C.O.R.E. is equipped with a gleaming, 24-inch, multi-touch display in elegant black. “You can see the process overview even from a distance,” says Liliane Schmid-Funke, who was involved in user experience design. Gone are the days of being bewildered by umpteen tiny numbers in gray boxes and an antiquated keyboard. The C.O.R.E. user interface features self-explanatory icons similar to a smartphone and is among the most modern in the machine tool industry, explains the graduate industrial designer. Furthermore, the large display can even be operated while wearing gloves.
During the development of C.O.R.E., the user was always the foremost consideration of the cross-brand development team when implementing functions, says Urs Diergardt, Head of User Experience. He adds that discussions with customers and within the team resulted in two different philosophies that had to be reconciled: on the one hand, experienced operators want to have control of all areas of the machine. On the other, the younger generation wants to work with smart and intuitive computer systems. And C.O.R.E. combines both of these approaches. “If you wish to, you can continue working as before. But using the new features will make your work more fun and increase efficiency.”
So what exactly are these functions? Andreas Meier, C.O.R.E. Team Leader for Software Development, explains: “Now, multiple users can create separate profiles on the same machine and customize the layout of the panel for themselves.” The system also features special user roles and permissions: users with programming knowledge can perform the more complex machine set-up tasks in the lower software levels for different workpieces and usage profiles.
Last but not least, C.O.R.E. is compatible with all CNC control units made by the UNITED GRINDING Group and the display can be simply switched to the native CNC interface at any time. However, operators can remain in the intuitive C.O.R.E. layout during day-to-day work. “The resulting system is clearer, meaning operators can familiarize themselves with the machine more quickly,” says Meier. This alone makes an important contribution to cutting costs and reducing the error rates in any facility. And if you have any questions, expert remote support is quickly on hand via video call right on the display.
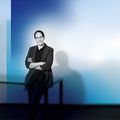
Find your way around on any machine thanks to C.O.R.E.
But C.O.R.E. can do much more. “Anyone familiarizing themselves with a new machine from UNITED GRINDING can also easily find their way around other machines with C.O.R.E. technology thanks to the standardized user experience,” explains Tobias Grimm, Software Developer at WALTER. This is a huge advantage for customers with multiple machines because C.O.R.E. can link them thanks to an integrated, high-performance industrial PC. C.O.R.E. machines can even exchange data with third-party products via the integrated umati interface (universal machine technology interface).
C.O.R.E. can do all of this already and makes work more efficient, faster, and easier. However, Alexej Berger, Software Developer at BLOHM and JUNG, knows that it is equally important that customers continue to be well-positioned in the future. “We are currently developing further updates and applications,” he says, “which will run on all UNITED GRINDING machines thanks to the uniform architecture.” What exactly can we expect here? Marcus Köhnlein, Head of Digital Business, answers: “Although C.O.R.E. is already one of the most advanced systems on the market, we are still only at the beginning.
We are currently working on extensions for the coming years that will help our customers save even more money.” One major topic is Human Machine Teaming, i.e.: how can man and machine work together most efficiently? For example, if someone has 30 years of experience in grinding, the machine should learn from this person. A young person in training, on the other hand, will be grateful for guidance from the software. From intuitive communication via the touch panel, mobile phone messages, or voice control, there is a multitude of possibilities.
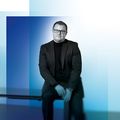
Perfectly prepared for a digital future
CTO Christoph Plüss also agrees that the C.O.R.E. journey has only just begun. “The trend towards digitalization will continue to pick up speed,” he says. Thanks to better data evaluation, grinding machines will not only be able to service themselves in the future, but also to communicate with other software. Interfaces to accounting or logistics departments are just one example. “The customer should be able to concentrate fully on their product—the machine does the rest.” Of course, customers must always have full control over what data they share with whom.
But it is certain that if you want to work more efficiently, simply, and cost-effectively today, there is no other choice but machines with C.O.R.E. It is pre-installed in all UNITED GRINDING Digital Solutions products and can be activated by purchasing a license. C.O.R.E. also provides remote support known for its quality and speed. This improves C.O.R.E. still further as the service specialists can access machine data directly when granted the appropriate authorization. This new technology perfectly prepares customers of the UNITED GRINDING Group for the trends of the future, such as increasing levels of digitalization and the more environmentally efficient use of resources. Thomas Bärtschi is a MÄGERLE software developer who attended EMO 2021 in Milan when C.O.R.E. was presented. In his words: “The positive feedback from our customers was absolutely overwhelming!”